How Temperature Monitoring Devices are Reshaping the Cold Chain
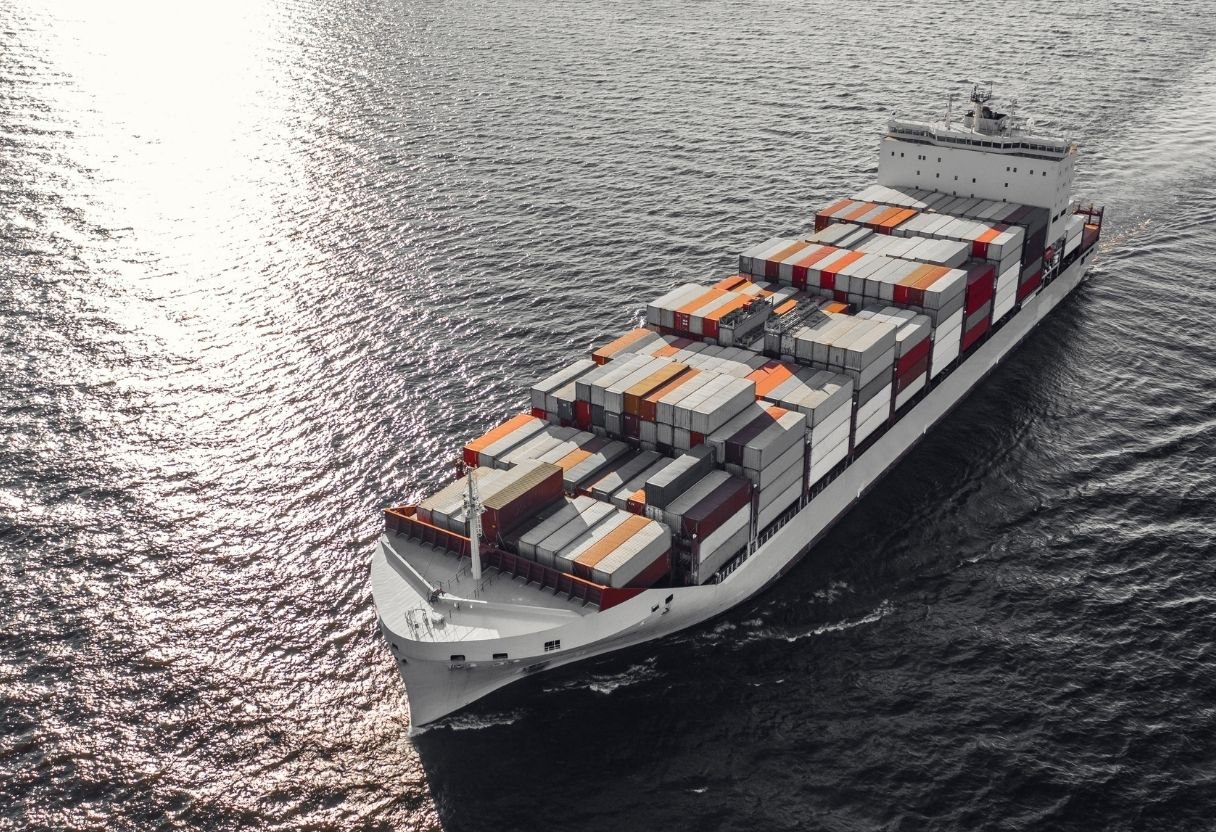
Temperature sensors are reshaping cold chain logistics for the better. Read on to learn how automation and real-time temperature monitoring are reducing product loss to create a safer and healthier world.
The cold chain is responsible for the movement of perishable food worldwide. While necessary to many people’s daily lives, it also has a painful secret: more than 20% of the perishable food transported within it spoils. However, this spoilage problem does not pertain to food only. Medical supplies such as COVID-19 vaccines are reliant on the strength of the current cold chain.
Improper food handling and data logging procedures and inadequate training for those working in the cold chain contribute to more than $750 billion of product loss globally in the food industry. In addition, $260 billion worth of bio-pharmacy sales depends on the cold chain for proper care for products in healthcare. WHO (World Health Organization) estimates that temperature control accounts for up 50% of vaccines wasted each year globally.
To combat this issue and those similar, distributors of all perishable items, food, and medicines included, are turning to IoT (internet of things) solutions, particularly temperature monitoring automation devices. Read on to learn how these new technologies optimize cold chain logistics to build a healthier and safer world.
Temperature monitoring redefined the supply chain.
To better conceptualize the breadth of the cold chain, look no further than the salmon in your freezer. Before arriving at your local Costco, the fish traveled thousands of miles through an intricate supply chain ecosystem of refrigerated ships and trucks, food processing plants, and distribution centers.
The ocean-to-table cold chain process exemplifies the incredible complexity and resources that fresh food needs to safely travel from its origin to our tables. The cold chain has revolutionized how we eat by making fresh fruits and vegetables available at all times of the year.
However, since the advent of shipping containers in the 1970s, safeguards and protocols to protect perishable items in the logistics industry haven’t progressed much. As recently as the 1990s, cold chain logistics still relied on styrofoam containers for temperature control in pharmaceutical products.
Human intervention is an essential factor in improving cold chain operational efficiency. Perishable items need exhaustive quality control throughout the distribution process. Some best practices include time detection, quality verification, and record-keeping to ensure quality at every stage of the supply chain. The earlier quality decay is detected, the better.
Real-time monitoring is the future.
The logistics industry began implementing real-time cold chain temperature monitoring devices in the early 2000s to reduce product loss events. These early temperature monitoring systems were primitive by today’s standards.
Typically, they involved wired sensors physically embedded into the infrastructure of cold storage facilities. This approach was not always practical due to high cost and lack of mobility, which curbed mainstream adoption.
Current digital temperature monitoring systems rely on wireless sensors connected through the Internet of Things, better known as IoT. IoT is the systematic connection of tools and devices linked together by the internet.
IoT monitoring devices automate the measurement of temperature, humidity, or other factors such as energy or light in your cold storage equipment.
The IoT sensor compiles data in the cloud and uses software and machine learning to create visual displays and features such as automated alerting and reporting. These advanced features are crucial in reducing pre-consumer product loss.
GlacierGrid is one notable temperature monitoring and analytics platform that has the opportunity to make a real difference in the cold chain. Powered by LoRaWAN, GlacierGrid is an IoT device that combines seamless wireless connectivity with up-to-the-second notifications and reporting. The result is a system that ensures your perishable products are of optimal quality and the right temperature, keeping vendors and clients alike happy.
How IoT technology promotes sustainability in the cold chain
One of the most significant concerns within the wider cold chain industry is sustainability.
The reason is the sheer number of resources needed to hold and transport perishable items, from the diesel and jet fuel required to transport them to the energy needed to store them.
IoT technology, particularly monitoring devices, reduces the likelihood that product waste will occur. Predictive responses to the leading causes of product spoilage, such as temperature excursions, and logistics providers can reduce the resources necessary to make the cold chain more effective and sustainable.
One example is in the prevention of refrigerant gas leakage. The chemicals used to power cold storage equipment are notoriously destructive. Refrigerant leakage in US supermarkets alone is equal to the use of 12.5 million cars annually.
Luckily, the symptoms of a refrigerant leak are often similar to those that cause food spoilage, I.E., slow, continuously warming temperatures within cold storage. Temperature sensors can quickly identify these occurrences, leading operators to take proactive measures to limit the damage caused by leakage.
GlacierGrid can help you automate temperature monitoring.
GlacierGrid is used primarily in places where spoilage tends to occur. These include cold storage warehouses, manufacturing facilities, food service businesses, and logistic hubs. A great example of how wireless technology can preserve food quality and reduce product waste is Moonstruck Chocolates in Portland, Oregon.
In high-end chocolate production, temperature and humidity conditions within production facilities need to be continuously monitored to provide high-quality output. During the manufacturing process, the chocolate is cooled from 113 to 82.4°F (45 to 28°C) before being heated to 86°F (30°C). After manufacturing, the chocolate must hold between 55 and 68°F (13 and 20°C), at 55 percent humidity, and without natural light exposure.
Moonstruck Chocolates implemented remote monitoring throughout its manufacturing process. Beginning with the storage of the raw materials, Moonstruck employs wireless sensors in locations close to the entryways wherever they store chocolates. Entries tend to be where warm air permeates due to an event like inventory loading or unloading. Alerts allow the operators to watch conditions and ensure the products do not deteriorate in substandard conditions.
Moonstruck uses remote monitoring solutions to manage ambient conditions down the line during production. Sensors at the four entryways of the production line room continuously report ambient conditions. Such tracking is important because the processing requires precursors in their original chemical state to be heated from a solid to a liquid, then back to a solid.
In their retail sites, Moonstruck monitors the conditions of their display cases and reach-in refrigerator; this is important because the appearance of the chocolate is almost as important as quality assurance in the production process.
Read more about Moonstruck’s experience with remote monitoring here.
Digital temperature sensors and the continuous evolution of the cold chain
While Moonstruck provides a good use case for temperature devices like GlacierGrid, the truth is that every foodservice business needs automated temperature monitoring. If you’re thinking about employing a temperature monitoring device in your distribution center, manufacturing facility, cold storage warehouse, restaurant, or any other business that deals with cold chain management, consider GlacierGrid.
GlacierGrid is a wireless temperature monitoring and analytics platform built with the food industry in mind. Our system is easy to install and provides up-to-the-second alerting and verifiable reports to protect your inventory and bottom line.
Click below to see how GlacierGrid can help your business operate more efficiently using digital temperature sensors.